Experience, collaboration, and attention to detail – these proven capabilities are integral to Fujifilm delivering the best metal complex conductive inks, as silver ink manufacturing expert Amanda Velez explains.
“As a company, we can adapt, work as a team, and put quality first. We’re efficient at doing that, which is why we’re able to keep up with a fast pace of development”, Amanda Velez, Silver Ink Manufacturing Supervisor
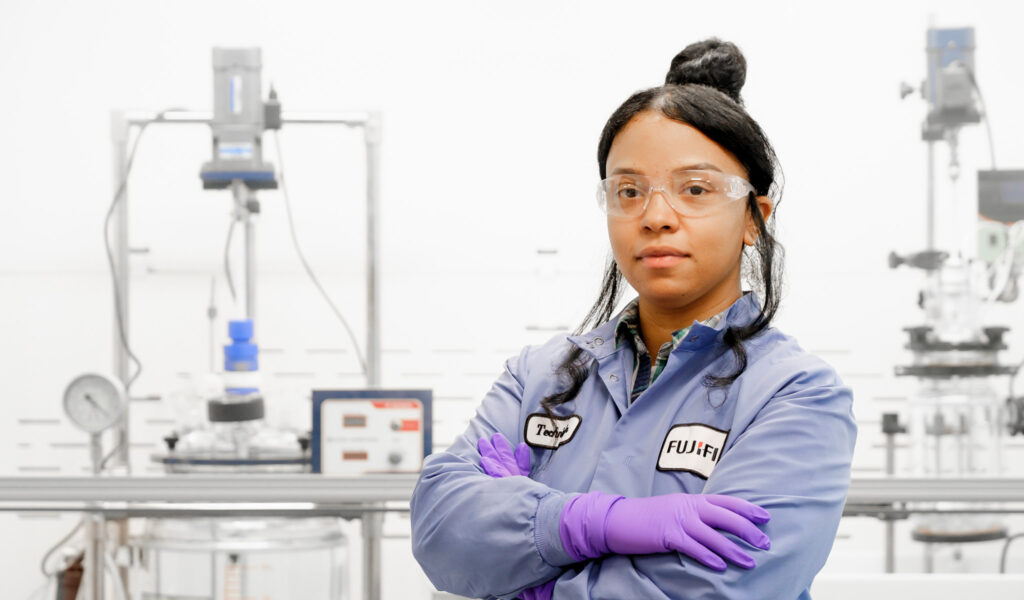
Ink manufacturing is highly collaborative. Excellent communication and a heavy emphasis on quality help us deliver the best results in complex silver inks manufacturing. But what’s different is our team-collaborative approach and the transfer of proprietary silver ink-making technology to our inkjet manufacturing facilities in New Castle, Delaware, under a contract manufacturing (OEM) agreement.
Managing the unique challenges of silver ink
Silver is a specialty conductive ink that final customers use for various applications, such as circuit boards and semiconductor packaging, and it’s unlike anything we’ve worked with before. So, it meant starting from the ground up.
As an ink manufacturer, our plan is for everything to be perfect. We strive to create the highest quality ink, whether aqueous or conductive. We began by testing some of the silver ink product’s parameters, ensuring we could take the customer’s formulation and transfer it to a small batch before scaling up. Although silver is a fantastic product, it has given us several challenges. Environmentally, it’s a dangerous material, requiring hand-in-hand work with our environmental team. In addition, the raw material is expensive, so we order when needed rather than holding inventory.
The shipping of silver ink is very different
We collaborate on-site with our quality assurance, environmental, shipping and supply chain teams looking at and working with the raw material. Next comes the ink-making and managing the daily making of batches and testing them.
An essential part of the quality process is collecting data and uploading it into our quality assurance system, grading any product before it can be released. Then, once the product is ready to be shipped to a customer, we work with our warehouse and shipping teams to ensure it’s packed, shipped cold, and stays cold.
The shipping of silver ink is very different from other inks because cold can ruin the product. Our Design of Experiments led us to develop a method of packing cold packs into the box for shipment to keep it for up to four days and ensure the ink’s integrity.
Excellent quality control for silver ink manufacturing
When manufacturing silver ink, there’s less room for error than doing a batch of aqueous inkjet inks where you can rework or recalculate an over or undercharge. With this high-value product, it depends on the order of addition. When you add something, it can’t be taken out, so there’s less wriggle room regarding the formulation or undercharge. It must be made right the first time.
Silver ink has a high purity specification, so we rely on our excellent quality control and inspectorate to check purity before ultimately shipping it to the customer, ensuring all the documents are in place for dangerous goods and hazardous materials.
Expertise feeds into attention to detail
I’ve grown with the company, experiencing different aspects of ink manufacturing and various departments. For me, manufacturing silver ink was a fresh opportunity to take over something new, develop methods, procedures, and processes.
Our expertise and culture of innovation, collaboration, and teamwork, where we hold ourselves accountable to the customer, have led to great feedback from our customers. And we keep the lines of communication open to learn how the ink worked for them. It’s not just a product to us – it’s a relationship we develop with our customers.