Global partnerships and a focus on product perfection help chemists and technicians to excel at UV inkjet development at Fujifilm’s research and development center in Broadstairs, UK, says technical manager Angelique Runacre.
“Some people are interested purely in science, but I’m more interested in the product being right at the end”, Angelique Runacre, Technical Manager
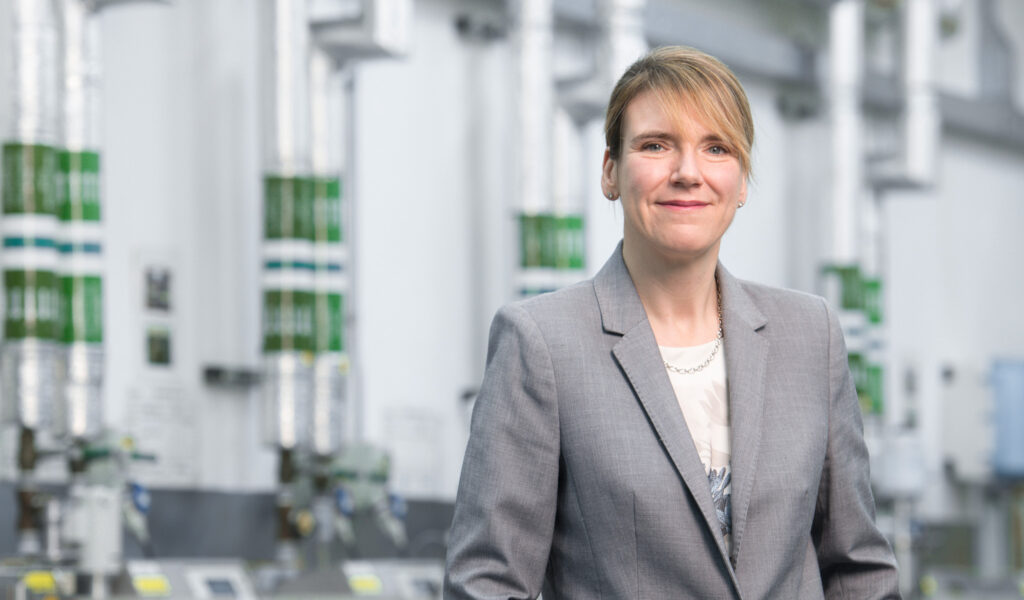
Collaboration is the main factor in ink development. We have excellent relationships with our OEM customers, and we collaborate internally to ensure we deliver ink solutions in the best way.
UV inkjet development for packaging
As the leader of a team of chemists and technicians, my focus is UV inkjet development for packaging applications, which is exciting ground for us. I’m also responsible for flexographic analog product development as more industrial applications need a hybrid approach.
The industrial and packaging markets are fascinating as there is an excellent opportunity to digitize many analog processes in the future, including both aqueous and UV. As well as the cost-saving and sustainability aspects of UV inkjet, the technology space is ready for development. Therefore, it is vital that we work to understand market segment issues and how we can help by providing a UV-curing inkjet technology solution. In tandem with this, we are working with raw material and hardware suppliers to develop the materials and systems needed to make inkjet a viable option for these new market areas.
Closing the gap between ink formulation and the print system
Having the resources of a global company to do my job and deliver is enjoyable. In the UK, we work closely with application development and applied integration teams who bridge the gap between ink formulation and the print system. In addition, we’re supported by excellent in-house intellectual property and regulatory support teams. We also work closely with our Japanese colleagues in ink development and developing novel raw materials.
I add the most value in a project’s early stages when working with the customer, whether an OEM or an end user, new concept development or internal technology development. With ink design, it’s about understanding the application area and where to maximize it. I enjoy working alongside our commercial and application teams to understand the specification and what we’re trying to do.
Once our R&D team is working to that specification, I will challenge the technical team to ensure we achieve that goal and encourage a broad view of technologies we could use – it may be something we’ve already got or is in development. Then it’s using that technology to meet the specification.
Inkjet inks go through a rigorous robustness check
In a development, we work closely with our applied integration team, application development team and the OEM’s technical teams. We’ll focus on whether the ink has the right quality to take it through to production. There’s no point in having the world’s best technical product if it’s unusable because it’s not robust, so the inkjet inks go through a rigorous robustness check. Then we work with our operations teams to develop the processes for manufacture. Operations and quality assurance teams support the ink during its lifetime, with our chemists available as advisors.
It’s great to see the business grow from the pioneering days of inkjet 20 years ago, when I worked on the development of high-end flatbed inks, to it becoming an established technology.
Fujifilm is a fantastic place to work, with lots of opportunities. My background at university was biochemistry, but through the company, I did a Masters in color chemistry. I also did an MBA, which helped me move into industrial areas and understand commercial opportunities. It’s supportive to speak the common language of the commercial teams and look at the technology that fits and where I can add value.
UV inkjet ink means lower energy consumption
The biggest challenge for me now is regulation and sustainability. I’m excited about what it means for ink development and its applications because inkjet is fantastic from a sustainability viewpoint – UV inkjet ink means lower energy consumption because you don’t need to drive off loads of water to dry your ink.
In digitized markets, such as signs and displays, inkjet is becoming increasingly important as a sustainable printing method. As well as reducing CO2 overheads associated with set-up time, it further minimizes the CO2 impact by lowering set-up waste and surplus stock disposal as you print on demand. We can also do our bit in product design to incorporate bio-based materials to reduce our product carbon footprint and build in the capability to recycle or compost.
Inkjet for UV applications, a real future
On the regulatory side, legislation is evolving as we speak. I’m fortunate to represent the company at the European Print and Ink Association and the British Coatings Federation, building our understanding of current and upcoming legislation. Being in our trade association means we can fight our customers’ corner and ensure sensible legislation. That’s truly valuable.
Inkjet for UV applications has a real future. The excitement lies in the opportunity – that’s where I want to add value.